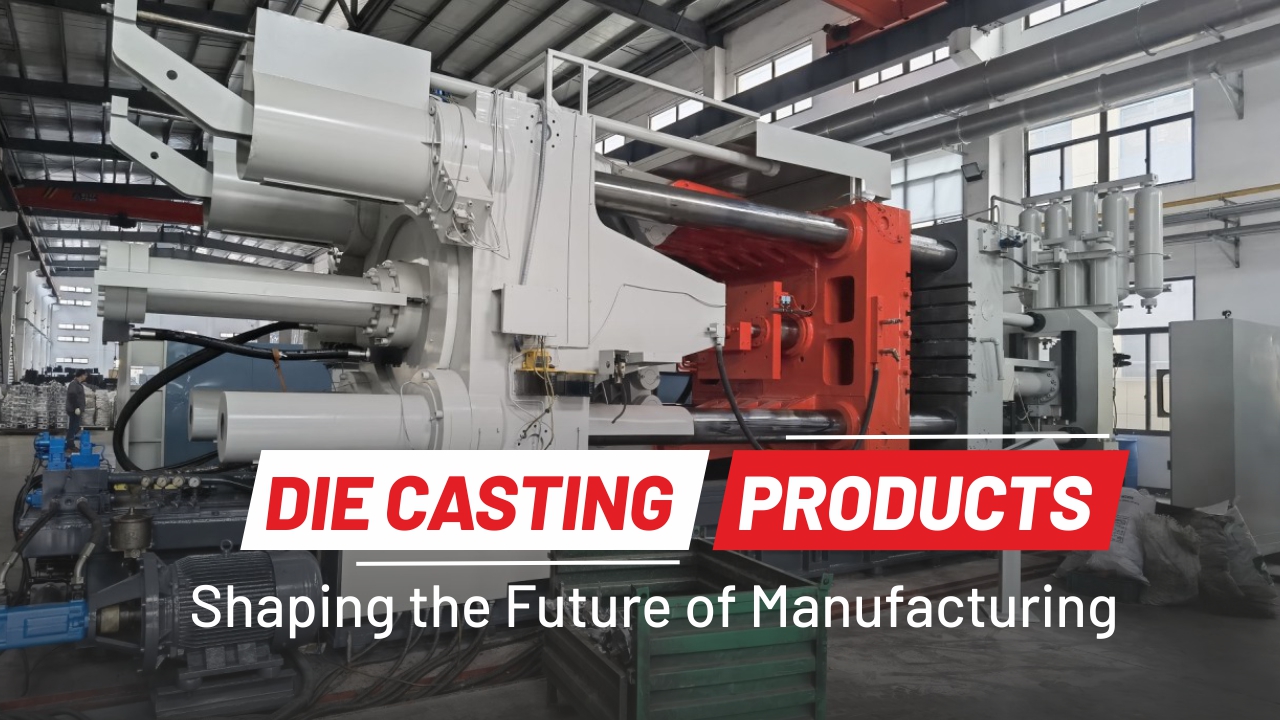
Die casting is a metal casting process used for the production of high-quality and precision parts that are made from non-ferrous metals like zinc, aluminium, and magnesium. Die-casting parts in recent times have become a good alternative for diverse materials, especially for industries that require consistent and precision parts having high dimensional accuracy. This has further made die-casting products ideal for diverse industries such as automotive, aerospace, and consumer electronics. Die-casting is an ideal solution for manufacturing bulk quantities of metal parts that have a high tolerance and are known to deliver exceptional performance.
What Is Die Casting?
Die casting is a manufacturing process through which metal parts are made with a high degree of precision. In this process, molten metal is injected into a steel mould or die, where it cools and hardens to create the desired shape. The mould comprises two halves, one is fixed and the other is movable and it is designed with intricate details to achieve high precision parts. This method is employed to produce various metal parts, from engine blocks and gears to electrical components and door handles. The best thing about this process is that it produces parts with a smooth surface finish and accurate dimensions. It is a highly cost-effective and fast process, hence making it attractive for diverse applications. High-quality die-casting parts have become a good replacement for diverse materials, as industries can obtain quality and durable parts at a reasonable cost.
How is Metal Parts Made with Die Casting Process?
The die-casting process comprises several steps including mould design, preparing metal, injection, casting, and finishing.
Mould Design – The initial step of the die-casting process is to create a mould or die that is generally made from steel and aluminium and can withstand high pressure and temperature during the die-casting process. The designing of the mould starts with developing a CAD design of the required mould that is later on used to create mould through CNC machining, which is later used in the casting process.
Metal Preparation – In the next step metal, which is usually an alloy like zinc, magnesium, or aluminium, is prepared by melting it into a furnace and then poured into a ladle.
Injection – The liquid metal in the molten state is injected into the mould under high pressure. The molten metal is poured into the mould cavity which creates the desired shape on cooling.
Casting – After the metal takes the desired shape after hardening, the mould is opened and the part is ejected. However, while casting it is essential to ensure that the mould is completely cooled before handling the mould to prevent any potential injuries.
Finishing Process – The last and final step in the making of die-casting products is the finishing, as surface finishing is vital in die-casting parts because it impacts the durability and functioning of the parts. The standard finishing process of die-casting products includes anodizing, powder coating, wet plating, etc.
Key Properties of Die-Cast Products
Die casting has emerged as one of the most efficient and cost-effective methods to produce metal parts on a large scale. This process though has been around for years but has gained popularity in recent years with manufacturers looking for ways to reduce production costs. Some of the key properties of die-casting products include:
High-Dimensional Accuracy – The die-casting process produces metal parts with high tolerances, thereby reducing the need for secondary machining. Thus, parts made with this process have high dimensional accuracy.
Excellent Surface Finish – Metal parts made with a die-casting process have smooth surfaces, making them suitable for undergoing further treatments like painting or plating.
Lightweight and Strong – Parts made with this process have an excellent strength-to-weight ratio, making die-cast products ideal for lightweight applications.
Corrosion Resistance – Die-cast products made of zinc and aluminium alloys show natural resistance to corrosion, extending product life.
Cost-Effective – Once the mould is created for making die-casting products, several identical parts can be quickly produced at cost-effective costs.
Applications of Die Casting Products
Die-casting products are used in a variety of industries and applications, some of the common applications of die-casting products include:
Automotive Industry – To reduce vehicle weight and improve fuel efficiency, the automotive sector greatly relies upon die-casting products such as steering housings, engine blocks, transmission cases, and brackets. In electric vehicles, aluminium die-cast products are used to enhance performance and energy efficiency.
Aerospace Industry – The Aerospace sector requires low-weight precision parts like complex airframe components, brackets, and housings that lower the weight of the aircraft without compromising strength and durability. Magnesium and aluminium die-cast products are usually required in the aerospace industry.
Electronics and Electrical Industry – Die-cast aluminium products like heat sinks, housings for LED lights, and enclosures for mobile devices are used in the electronics industry, because of their excellent thermal conductivity. This allows die-cast products to effectively dissipate heat and ensure the longevity of electronic components.
Summary
Die casting is shaping the manufacturing landscape by offering precision, efficient, and versatile products. The demand for die-cast products is growing rapidly across various industries, ranging from automotive and aerospace to consumer electronics. With industries embracing lightweight and sustainable products, die casting plays a vital role in producing high-performance parts that meet the evolving demands of modern manufacturing. The future of die-cast products looks promising, offering endless possibilities for innovation and growth.