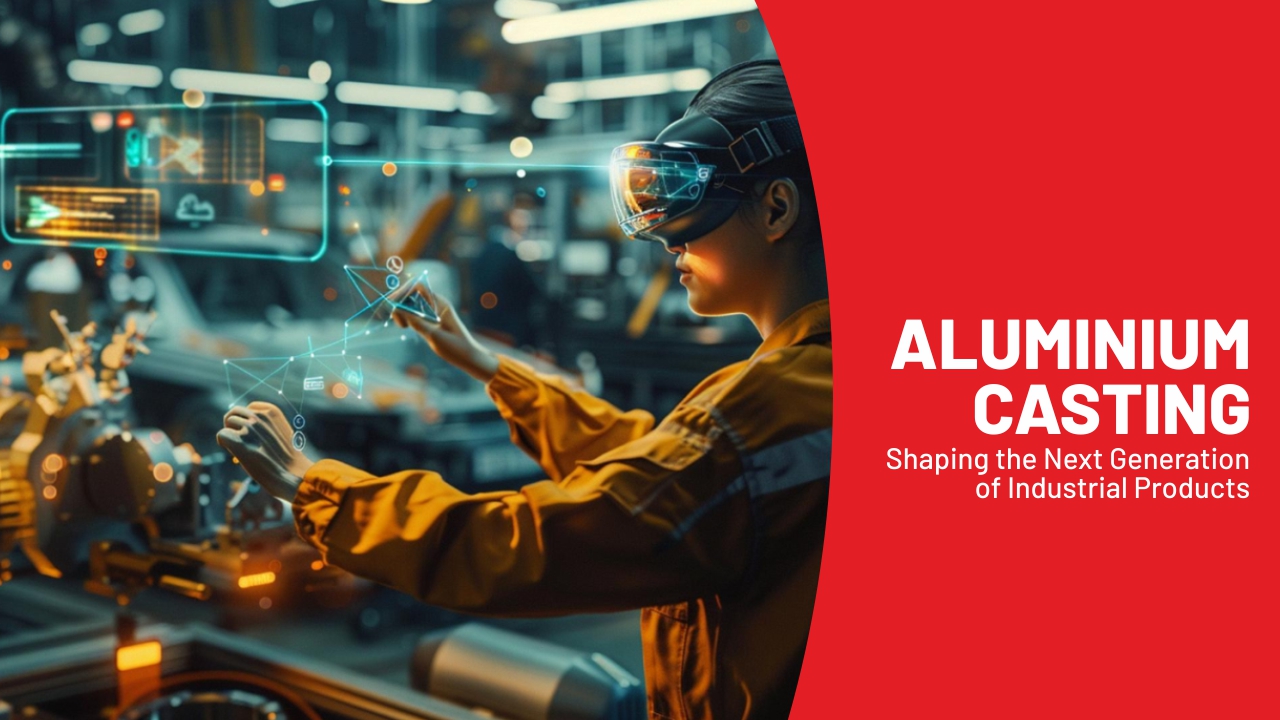
The market size of aluminium die casting was valued at USD 33.01 billion in 2024 and is projected to reach USD 64.99 Billion by 2031. The surge in demand for aluminium die-cast automotive parts is primarily because of the emphasis on reducing vehicle weight in the automotive sector. To fulfil stringent fuel efficiency and emission standards, automotive manufacturers are increasingly relying on aluminium die casting to produce complex auto parts while maintaining structural integrity. Another factor that is driving the growth of aluminium die-cast parts is the adoption of electric and hybrid vehicles that require lightweight components to maximize range and fuel efficiency. In addition to this, the growing consumer demand for advanced safety features and enhanced driving experience has also led to the growing integration of aluminium die-cast parts in transmission systems, suspension components, and automotive chassis. The increased use of aluminium die-cast auto parts has propelled the expansion of the global market and is encouraging manufacturers to innovate to enhance production processes and meet the requirements of the evolving industry.
The Aluminium Casting Process
Aluminium die casting is a manufacturing process used to produce complex and lightweight aluminium components that are used across automotive and various other industries. In this process, molten aluminium is poured into a steel mold under high pressure to create precise and complex aluminium parts and components. In die-casting process aluminium ingots or scrap is melted at temperatures around 660°C and the molten aluminium is poured into intricate mold cavities and left to solidify. After the metal solidifies, the finished part is removed from the mold and may require some processing like trimming, polishing, or machining to create high-quality, durable, and lightweight components. The parts created through this process are a fine blend of strength, lightweight, corrosion resistance, and recyclability, making it a popular choice for a wide range of industries, from automotive to consumer goods to aerospace and construction. This process is known for creating parts with dimensional accuracy, excellent surface finish, and structural integrity.
Key Aluminium Casting Methods
Different methods are employed for aluminium casting and the right method or process is selected depending on the project’s requirement and the parts that have to be made. Every casting process has its own set of benefits and advantages and is chosen based on the type of parts that have to be manufactured. Aluminium die casting is a process in which molten aluminium is injected into molds to produce complex, high-precision parts. The three main processes are:
High Pressure Die Casting (HPDC) – In this process molten aluminium is injected into a steel mold under high pressure i.e. up to 1,500 bar. The parts or components created have excellent surface finish, precise dimensions, and intricate designs. This process is ideal for high-volume production and provides strong, durable products for automotive engine blocks, transmission cases, and electronics.
Low-Pressure Die Casting (LPDC) – In low-pressure die casting aluminium is forced into the mold using low air pressure from the furnace below. It is usually an automated process that has better control over metal flow. The parts produced through this process have high quality and improved mechanical properties with fewer defects. Besides, the parts also require minimal finishing or trimming and this process is employed to produce automotive parts like wheels, cylinder heads, and aerospace parts.
Gravity Die Casting (GDC) – In the gravity die casting process, molten aluminium is poured into the mold under gravity, without applying any external force. It is a low-pressure casting process that relies on gravity power to fill the reusable molds made of iron or steel. This process is ideal for producing parts with good strength, excellent surface finish, and minimal porosity. It is an economical process that requires less energy compared to other processes and is used to produce auto parts like engine cylinder heads, intake manifolds, and automotive transmission housings.
Benefits of Aluminium Casting
Aluminium cast products are popular across diverse industries, as they offer significant advantages over other materials. Some of the reasons behind their popularity across industries include:
Fine Surface Finish – Aluminium cast products and parts have a smooth and silvery appearance, eliminating the need for an expensive surface finishing process.
Lightweight and Durable – Aluminium parts are light in weight compared to parts made from steel or other metals, without compromising on strength, durability, and other mechanical properties.
Corrosion Resistance – Aluminium parts have a natural oxide layer that protects them from corrosion.
High Thermal and Electrical Conductivity – Aluminium can bear high temperatures making it ideal for heat sinks and electrical enclosures.
Design Flexibility – Casting allows for the creation of complex shapes that would be otherwise difficult to create or expensive to make using other methods.
Recyclability – Aluminium is 100% recyclable, making it an ideal choice for manufacturers.
Applications of Aluminium Casting in Industry
Aluminium cast parts and components are used across diverse industries due to their excellent physical and chemical properties. Being strong, durable, and lightweight, the aluminium cast parts and components are used in the following industries:
Automotive – Aluminium casting parts like engine blocks, cylinder heads, wheels, and transmission cases are widely used across the automotive sector. Due to the aluminium lightweight properties, these parts help improve fuel efficiency and reduce emissions.
Aerospace – In the aerospace industry, aluminium casting process is employed to manufacture critical components like aircraft fuselage parts, landing gear, and engine components.
Consumer Goods – In the consumer goods industry, a wide range of products like cookware, furniture, and electronic housings are made from aluminium cast parts because of their good thermal conductivity, aesthetics, and lightweight nature.
Summary
Aluminium casting is a vital process used across industries due to its ability to produce lightweight, durable, and complex components. With continuous improvements in casting methods and the adoption of Industry 4.0 technologies, the future of aluminium casting looks promising. As the demand for sustainable and innovative manufacturing grows, aluminium casting will play a pivotal role in shaping the next generation of industrial products.