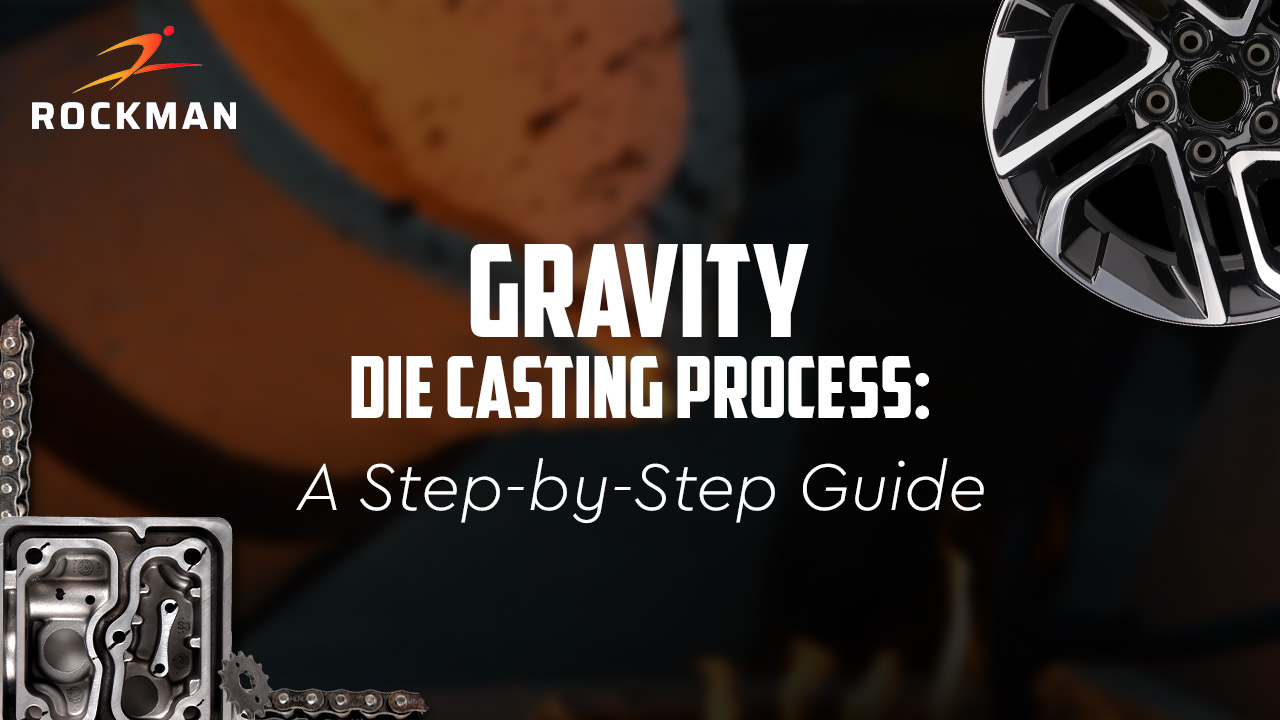
Gravity die casting is one of the most crucial processes in the production of high-reliability, long-life metal parts. This method is popular because it can generate parts with enhanced mechanical properties and small porosity in addition to being versatile for the automotive and engineering industries.
Being a leader in aluminium gravity die casting, Rockman has mastered this art to produce accurate components that fit perfection from the market. It is high time that we looked deeper into this process and learned as to why it has become so essential to modern manufacturing techniques.
What is Gravity Die Casting?
Gravity die casting is amongst the most effective methods in which molten metal is poured into a permanent metal mold with the help of the force of gravity. Unlike high-pressure die casting, this process only uses the force of gravity in order to feed the mold cavity. This method is quite applicable when manufacturing bulky to moderately small complexity parts that require a balance of strength, accuracy, and cost.
At Rockman utilizing the aluminium gravity die-casting process, we embrace advanced technology that allows us to deliver high-quality casting parts. Products produced through this process are being used in various industries to show they are very reliable and have good endurance.
Step-by-Step Guide to the Gravity Die Casting Process
1. Designing the Mold
However, it is important to understand the process of gravity die casting in order to appreciate the enterprise that goes into creating a solid mold that is still reusable. As a mold maker Rockman specialty is to create molds to meet specific standards for functionality of the finished product in terms of size and other characteristics. Commonly constructed from steel or iron, the mold is designed to last several uses or shape matter without deforming under heat.
2. Preparing the Mold
Mold preparation is done before pouring. They coat the surface of the system or part that they want to produce through casting, and a release agent or lubricant is applied to ensure the cast component does not stick. This step is very important to produce a good surface finish on the mold and to increase its cycle life.
3. Melting the Aluminium
Rockman deals with aluminium gravity die casting and uses high-quality aluminium alloys. The aluminium is then recycled by melting it in a furnace at predetermined temperatures and conditions in order to achieve the requisite quality. Effective control technologies help to achieve an ideal temperature for the molten metal to be cast.
4. Pouring the Molten Aluminium
When the aluminium is ready, it is then poured into the mold which is then prepared properly. When the molten metal is distributed evenly and doesn’t need force to pack the mold cavity, gravity plays a part in the pouring process. This process minimizes interference and hence the chances of having the wrong porosity or poor solidification as well.
5. Cooling and Solidification
The aluminum starts to cool and when it does, it sets to the specific form of the mold that it has been placed in. On the other hand, Rockman’s cooling methods are strategic to control the rate of solidification and improve the mechanical nature of the cast component. Even cooling also reduces internal stress while enhancing the dimensional stability of the final product.
6. Removing the Casting
At the end of the process, the casting is carefully taken out of the mold once the material has solidified. Afterwards, the reusable mold is inspected and gets ready for the next cycle. In addition, all component parts that are produced at Rockman are inspected to the highest level of quality.
7. Finishing Processes
Following removal, the casting undergoes a number of finishing operations including reduction in size by trimming, and alteration of size by accurate cutting or boring known as machining. These steps are not general steps but are developed to suit the needs of the application in question. Its finishing capacity makes Rockman capable of providing every component as per usage, performance, and sturdiness.
Why Choose Aluminium Gravity Die Casting?
Aluminium gravity die-casting is preferred due to its benefits of creating lightweight, high strength and resistant to corrosion parts. At Rockman, this process is further enhanced through:
Precision Engineering: High-quality equipment and qualified staff guarantee that every component is created according to the specified parameters.
Cost Efficiency: The molds are reusable molds and efficient processes, making it an economical choice for medium to high-volume production.
Environmentally Friendly Practices: Rockman places a strong emphasis on environmentally friendly production methods that use less energy and produce less waste.
Applications of Gravity Die Casting
Gravity die casting is one of the versatile processes which are used to manufacture many types of components. Rockman caters to industries requiring high-quality aluminium gravity die casting, including:
Automotive: Valves, gearboxes, camshafts, cylinder heads and blocks, pistons, wheels, gears, axle housing, frames, and brackets.
Industrial Equipment: Durable parts for equipment and instruments used in the industry.
Engineering: High-quality components for requirements in engineering applications.
Rockman: A Trusted Partner in Aluminium Gravity Die Casting
For over thirty years, Rockman has been an icon of aluminium gravity die casting. It is these values that make us stand out: innovation, quality, and satisfaction of customers.
Here’s what makes Rockman a preferred choice:
Cutting-Edge Technology: We use advanced method technology and tools of the highest quality to produce the parts.
Custom Solutions: Our services offered to the clients are custom-made right from the initial design to the final delivery.
Rigorous Quality Control: Each of the steps described is closely observed to make certain that they are comparable and accurate.
Why Partner with Rockman?
By choosing Rockman for aluminium gravity die casting, you benefit from:
Unmatched Expertise: Having had the opportunity to serve our customers for decades, we’ve gained experience in delivering quality parts.
Sustainability Focus: We ensure each step is Environment friendly and integrate responsible practices.
Comprehensive Support: Rockman accompanies you from the moment of consultation to the moment when your ordered product is delivered to you.
Global Standards: Our products undergo the highest world standards in quality performance guaranteeing the best results.
Conclusion
Gravity die casting is still widely used as a modern day essential of the manufacturing industry since it allows for great accuracy, high strain and low cost. Our aluminium gravity die casting capability makes Rockman a valuable supplier and service provider of the global industries. The drive for innovation, quality, and sustainability is what defines, and enables us to build the future of manufacturing.
Join us and unpack the opportunities with Rockman’s aluminium gravity die casting options and see how we translate your vision into reality.