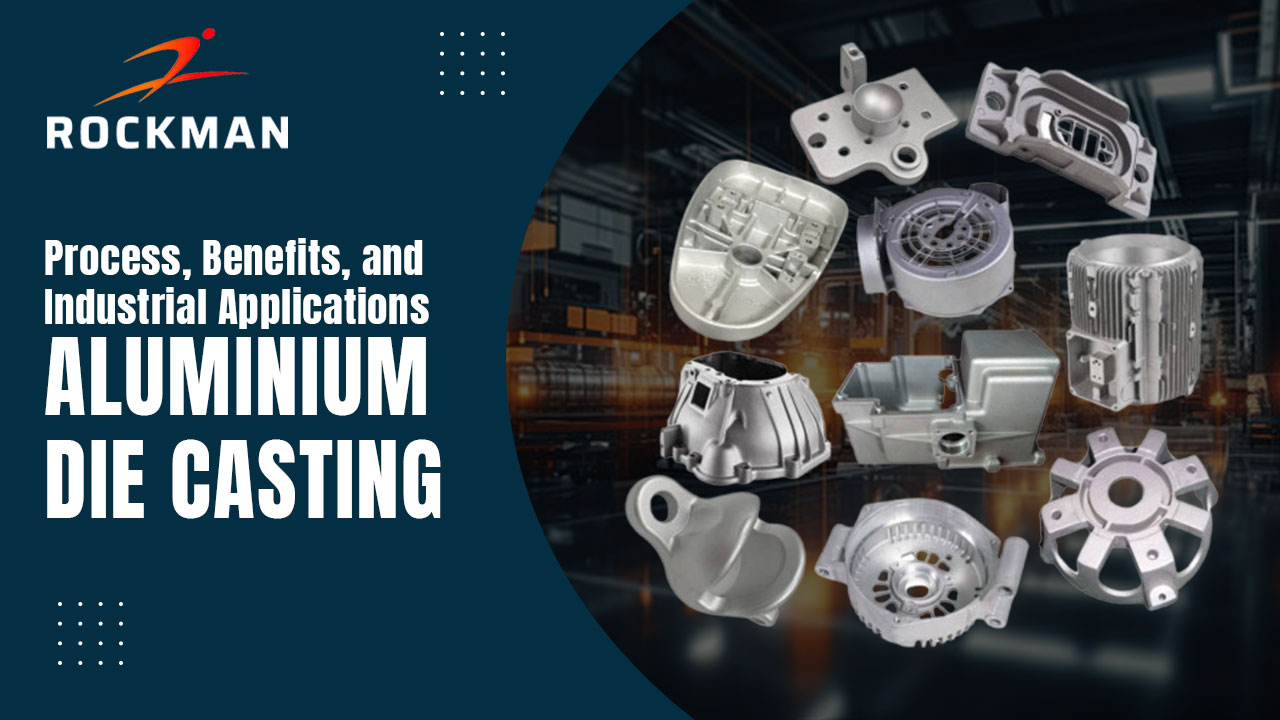
Die-casting parts are finding great relevance in industries that require strong, lightweight, high precision, and excellent dimensional accuracy components. These parts are particularly valuable across diverse sectors like automotive, electronics, consumer goods, and aerospace where parts with complex design and high tolerance are required. Die casting is a widely used manufacturing process producing precision-engineered metal parts having excellent mechanical properties. The best thing about the die-casting process is that lightweight components can be manufactured in large volumes at a cost-effective price. Identical parts in large quantities can be mass-produced at a quick pace. Die-casting parts are used across many industries due to their strength, surface finish, and dimensional accuracy.
Understanding the Die Casting Process
Die casting is a revered metal casting process in which usually low-melting points metals like zinc, aluminium, and magnesium are used. In this process, molten metal is forced under high pressure into molds or dies to create complex, durable components. After the metal solidifies the die halves are separated and the component is ejected from the dies using ejector pins. The parts produced are inspected for any imperfections or defects and may undergo additional finishing operations like trimming, machining, surface finish, and quality inspection to ensure that parts are manufactured as per the specifications.
Different Types of Parts Made with Die Casting Process
Die casting is a revolutionary manufacturing process adopted to produce intricate and complex metal parts that are used across diverse industries. These parts are highly versatile and can be tailored to meet specific requirements of the industry. Different types of parts and components that can be made using die die-casting process include:
Structural Parts – Die casting is a popular way to produce large structural components that serve as the framework like automotive frames or support in assemblies like machinery housings.
Precision Components – Automotive and electronic industries require precision parts that are of high dimensional accuracy and tight tolerances. Thus, the die-casting process is used to produce precision components like enclosures, gears, and heat sinks.
Small and Complex Parts – Die casting process leads to the production of parts with fine detailing and intricate designs like curved components, multi-hole fixtures, and small complex parts.
Thin-Walled Parts – The die-casting process involves high pressure that allows the production of thin-walled parts without compromising on their strength. Thin-walled parts are high in demand for lightweight applications like aircraft and consumer electronics.
Advantages of Die Casting Parts
Die casting process in recent times has gained huge popularity, as this process serves multiple benefits and turns out to be an ideal process for producing complex metal parts in high volume. This manufacturing process is ideally used to produce high-precision and dimensional-accurate products. Some of the primary advantages of die-casting parts include:
Excellent Dimensional Accuracy – Die-casting parts are known for having excellent dimensional accuracy. The molten metal is injected into the mould under high pressure, ensuring that it fills every contour. This ensures that the casted parts exactly replicate the mould design with the greatest precision and highest accuracy, even when parts are produced in large quantities.
Superior Surface Finish – Die-casting parts are known for having superior surface finishing compared to parts produced through other casting processes. Some of the parts don’t even require finishing, as these parts are ready to use just after trimming off the excess material. Additional finishing processes like grinding, machining, and powder coating are only required when there is a need for highly polished parts.
Fast and Bulk Production – Die casting parts can be produced in bulk quantity and at remarkable speed. Die casting machines once set can inject molten metal into the mould in just a few seconds depending on the size and design of the parts. Besides, the die-casting moulds can bear extreme temperatures and pressure that prolong the life of the mould that can produce hundreds of thousands of parts before the need to replace the mould.
Durability and Strength – Die-cast parts are durable and stronger compared to parts made by another process. Die-cast parts are usually made from metals like aluminium and zinc that have a fine balance of strength and weight. Die-cast parts have excellent mechanical properties, including durability and high strength. These parts withstand harsh conditions and are resistant to corrosion, temperature variations, along wear and tear.
Conclusion
Die casting is a vital manufacturing process used to produce metal parts or components that are used across diverse industries. These parts come with dimensional accuracy, cost-effectiveness, and high production speed. Its applications span across various industries, from automotive and aerospace to electronics and consumer goods. Although there are challenges in die casting, especially with initial costs and material limitations, advances in die casting technology are allowing overcoming these challenges. Die casting remains an excellent choice for manufacturers looking for a reliable, efficient, and high-quality process for manufacturing metal parts.